La PCB es el componente básico de cualquier circuito electrónico, independientemente de lo simple o complejo que pueda ser. El uso generalizado de componentes para montaje superficial (SMD), combinado con la necesidad de múltiples capas, ha aumentado inevitablemente la complejidad de las PCB actuales. Con independencia de la aplicación, el requisito común que deben cumplir todas las PCB es funcionar correctamente según las especificaciones del proyecto y carecer de defectos. Los circuitos electrónicos de última generación incluyen cientos de componentes con miles de soldaduras e interconexiones: por lo tanto, es esencial definir unos procedimientos de inspección y ensayo rigurosos, capaces de garantizar la calidad del producto final. Como consecuencia del reducido tiempo de comercialización y de la elevada competencia en muchos campos de la electrónica, algunos circuitos electrónicos pueden salir de la fase de prototipado con fallos o defectos que deberán ser identificados y resueltos antes de que el producto llegue a la fase final.
Resumen de pruebas PCB
Cuando los circuitos electrónicos eran relativamente sencillos, la inspección visual manual (MVI) era suficiente para detectar posibles problemas como cortocircuitos, uniones de soldadura imperfectas, trazados interrumpidos, polaridad invertida de algunos componentes o incluso ausencia de componentes. Sin embargo, la técnica de MVI no estaba exenta de problemas relacionados con los errores cometidos por las personas en la realización de operaciones aburridas y repetitivas. Esto ha creado situaciones en las que los defectos no se detectaron o se hallaron en una etapa muy avanzada del diseño, en la que las modificaciones del circuito ya resultaban demasiado costosas. El siguiente paso consistió en automatizar el proceso de inspección visual mediante la técnica AOI (Inspección Óptica Automatizada). La AOI es actualmente un método de inspección verificado, de uso generalizado tanto durante el preflujo como el posflujo de soldadura, y disponible en varias máquinas de recogida y colocación. El empleo cada vez más masivo de componentes SMD y de paquetes BGA (Ball Grid Array) ha puesto de manifiesto las limitaciones de la AOI, que ya no es capaz de detectar las conexiones y soldaduras ocultas en la parte inferior del paquete. Así pues, se desarrolló la técnica de inspección automatizada de rayos X (AXI – Automated X-ray Inspection), basada en el uso de rayos X capaces no solo de ver a través del paquete sino también de inspeccionar PCB multicapa con una alta densidad de componentes. Una vez superada la fase de inspección, la PCB se someterá a un test exacto, realizado en el circuito completamente ensamblado.
Objetivo de las pruebas PCB
Una PCB está compuesta de diferentes elementos, cada uno de los cuales afecta al rendimiento global del circuito electrónico. El conjunto mínimo de tests a realizar debe incluir las siguientes comprobaciones:
- Conductividad eléctrica, incluyendo la medición de las corrientes de fuga;
- Resistencia mecánica;
- Calidad de las soldaduras;
- Limpieza (resistencia a la intemperie, incluida la humedad y la corrosión);
- Calidad de la pared del orificio;
- Laminación, que prueba la resistencia del laminado al pelado por la fuerza o la aplicación de calor;
- Metalizado con cobre, en el que se prueba la resistencia a la tracción y se analiza la elongación resultante;
- Ensayo ambiental, especialmente para las PCB que funcionan en ambientes húmedos;
- Polaridad, orientación, alineación y colocación de los componentes.
AOI
Al tratarse de un método de inspección, la AOI puede detectar fallos o defectos de la PCB en una etapa temprana de desarrollo. La AOI es un método de inspección visual que utiliza cámaras para obtener imágenes de la placa desde diferentes ángulos y con distintas condiciones de iluminación. Esta técnica también integra la funcionalidad de OCR capaz de interpretar las serigrafías de la PCB. A continuación, las imágenes obtenidas se comparan con lo que se quiere conseguir (la denominada «placa dorada»). Este método presenta la ventaja de detectar diferentes tipos de defectos y puede utilizarse en varias etapas de desarrollo. El principal inconveniente es el de estar limitado a una línea de control visual, con lo que no se pueden comprobar las conexiones ocultas por BGA u otros tipos de paquetes.
AXI
La alta densidad introducida por la tecnología SMT y la incapacidad de identificar las conexiones en los paquetes BGA y CSP (Chip Scale Package), requería unos métodos de inspección más precisos, como los basados en rayos X (AXI). Dado que las soldaduras se realizan con un material cuyo peso atómico es superior al de los demás componentes de la placa, son claramente visibles en las imágenes radiográficas. La principal ventaja de la técnica AXI es que detecta todas las conexiones y soldaduras, incluso las que están ocultas por el paquete; además, también se pueden inspeccionar las uniones de soldadura, poniendo de relieve la posible presencia de burbujas. Las posibilidades de detectar cualquier falsificación de componentes electrónicos patentados también son significativas. Por otra parte, la técnica AXI es relativamente costosa y su inversión solo puede justificarse en el caso de PCB de alta densidad y los componentes con un paquete BGA o CSP. En la figura 1 se muestra un defecto detectado por inspección de rayos X.
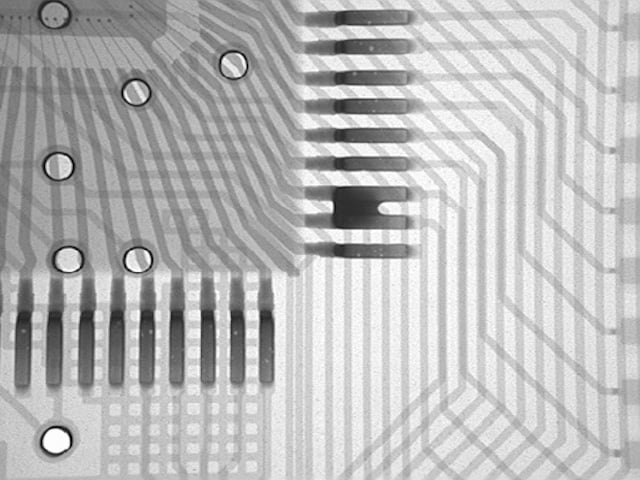
Figura 1: Defecto de la PCB detectado mediante inspección de rayos X
Prueba en circuito (ICT)
Este test, realizado después de la etapa de ensamblaje, verifica el correcto funcionamiento y posición de cada componente electrónico en la PCB. El test incluye la verificación de cortocircuitos, los circuitos abiertos, la resistencia, la capacitancia y otros parámetros. Para ello se utiliza una sonda volante, compuesta por un conjunto de excitadores y sensores que realizan las mediciones requeridas por el test moviéndose libremente en la placa. La sonda se controla mediante un software adecuado, que puede modificarse adaptando el mismo sistema de ensayo a placas con diferentes diseños. Como alternativa, se puede utilizar un banco de ensayo, que consiste en una base de clavijas diseñada para el dispositivo objeto de ensayo (DUT – Device Under Test) específico. Cada «clavija» se comporta como un sensor real, capaz de conectar eléctricamente un punto específico del DUT al sistema de ensayo. La base de clavijas es una técnica costosa y no demasiado flexible (cada placa requiere la suya propia); además, presenta ciertas dificultades a la hora de probar placas con alta densidad de componentes, en las que se reduce el espacio entre las clavijas. La técnica ICT reporta la ventaja de detectar varios defectos, relacionados tanto con los componentes individuales como con sus conexiones, y puede realizarse sin necesidad de alimentar la placa. Su inconveniente está relacionado con el coste (complejidad de la base de clavijas y del programa informático de control) y la imposibilidad de probar los conectores, lo que constituye una limitación significativa en los sistemas analógicos y digitales compuestos por varias tarjetas. En la figura 2 se muestra una máquina para realizar tests de funcionamiento (ICT) con una sonda voladora.
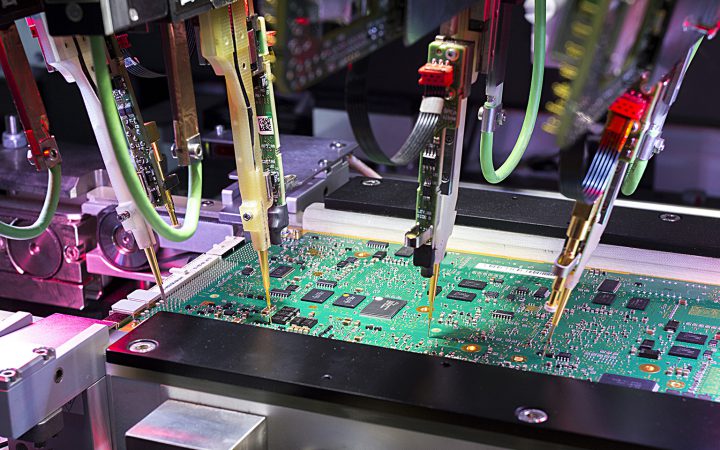
Figura 2: Test de funcionamiento (ICT) con una sonda voladora
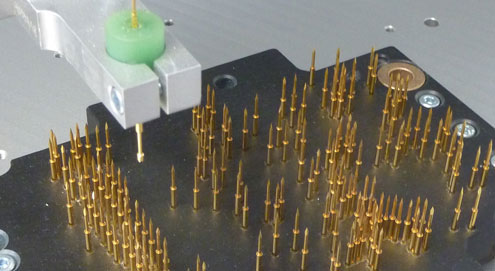
La figura 3 muestra un banco de pruebas personalizado, preparado para la ejecución del test de la base de clavijas
Test funcional
El test funcional es el último paso del proceso de inspección y verificación. Como su nombre indica, su tarea consiste en probar el funcionamiento de un circuito, reproduciendo las señales eléctricas capaces de estimularlo y midiendo los efectos producidos. El circuito está correctamente alimentado y estimulado eléctricamente a través de los conectores de la interfaz. Una aplicación informática procesa las mediciones realizadas en puntos adecuados de la PCB, verificando su correspondencia con las especificaciones de diseño. La ventaja del test funcional es su capacidad para detectar posibles anomalías del circuito que solo se producen cuando el circuito está alimentado; además, también es capaz de medir la absorción de potencia en puntos específicos del circuito. Los inconvenientes están relacionados con el coste y la complejidad del sistema de ensayo. De hecho, requiere un equipo muy sofisticado, pero no demasiado flexible, la mayoría de las veces configurado para realizar únicamente el ensayo de una tarjeta específica.
Escaneo de límites
El escaneo de límites es una técnica introducida para probar las interconexiones entre los componentes de la placa y se utiliza ampliamente para probar los circuitos integrados cuando no es posible el acceso a todos los nodos del circuito. Las sondas físicas se sustituyen por «celdas» cuyos pines de datos de salida (TDO) y de entrada (TDI) están conectados en secuencia a registros de desplazamiento adecuados y a un sistema de circuitos para su multiplexación. La lógica del escaneo de límites está temporizada por una señal TCK (Test Clock), mientras que una señal TMS (Test Mode Select) habilita el test. De este modo, es posible acceder a las entradas/salidas sin tener que colocar puntos de ensayo físicos en la placa, a través de una simple interfaz serie de 4 hilos (que se convierte en 5 si se incluye una señal de reinicio opcional) llamada TAP (Test Access Port). Los archivos del lenguaje de descripción de escaneo de límites (BSDL – Boundary Scan Description Language), proporcionados por los fabricantes, contienen información sobre los componentes del escaneo de límites. El método de escaneo de límites presenta la ventaja de ser adecuado para varias aplicaciones, incluyendo el test a nivel de sistema, el test de memorias RAM y flash y la emulación de CPU. Además, el test puede realizarse directamente in situ. Por otra parte, su principal inconveniente es que no se trata de un test exhaustivo, cuya cobertura se limita a los componentes que soportan este tipo de interfaz.
Conclusión
Independientemente del método elegido, las pruebas PCB representan un paso fundamental en el proceso de diseño electrónico, al ser capaces de ahorrar mucho tiempo y dinero, identificando los posibles defectos que afectan al circuito antes de que llegue a la producción final. En general, una combinación adecuada de los métodos de inspección y ensayo mencionados anteriormente puede detectar todos los posibles defectos, con unos costes variables que están en función de la aplicación y la complejidad específicas del circuito objeto de ensayo.